The XELTA Mix bags are designed for reliable and flexible large-scale applications in biopharmaceutical and pharmaceutical manufacturing. Made from premium film, these bags offer ease of use and efficient product recovery for handling large fluid volumes. They are available in various sizes and can be used for buffer, media, intermediate, or drug substance mixing. Customizable configurations are available to meet specific process requirements. Manufactured under ISO 9001:2015 certified quality management systems and cGMP conditions, the bags undergo extensive testing to ensure compliance with pharmacopoeia standards and bio-compatibility. The specialized multilayer film used in XELTA Mix bags provides excellent chemical resistance, including polar solvents, and has favorable properties such as clarity, tensile strength, and gas permeability. Gamma irradiation is the recommended sterilization method for these bags.
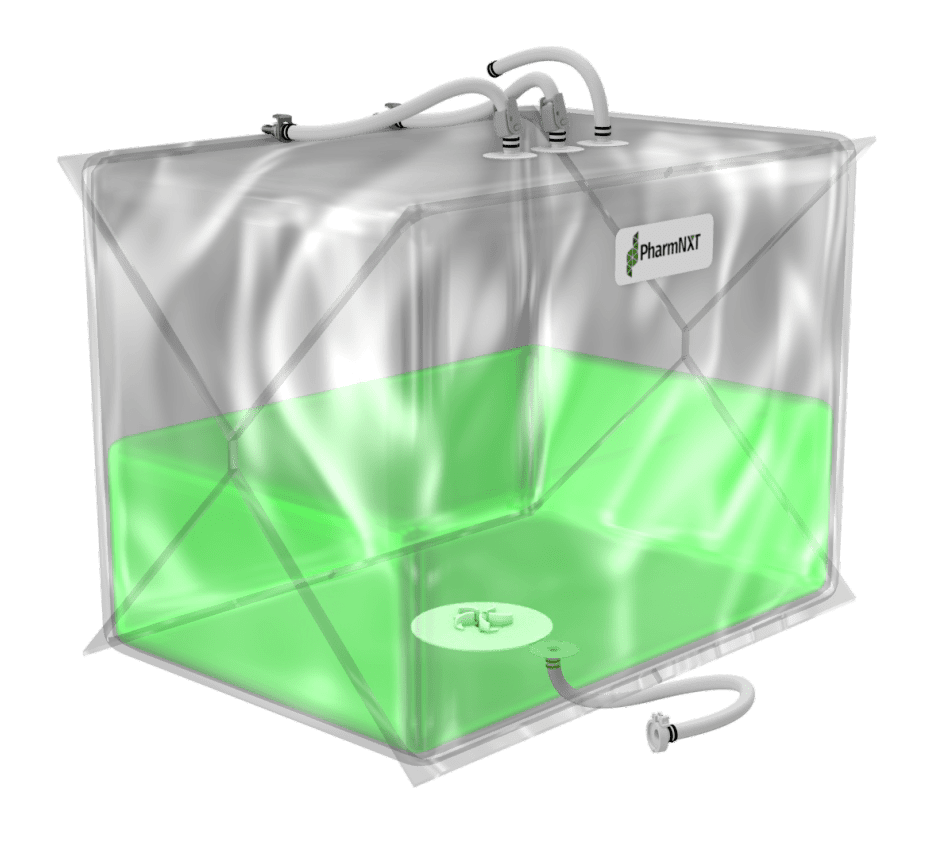
The XELTA Mix bags are designed for large-scale applications where systems are required to be reliable, flexible and easy to install. Manufactured from premium film Validated for use in Biopharmaceutical and pharmaceutical manufacturing processes. The XELTA Mix bags bring together state-of-the-art design features that improve the robustness of single-use systems. This brings considerable advantages in terms of ease of use and product recovery when dealing with large fluid volumes.
The XELTA Mix bags are designed for reliable and flexible large-scale applications in biopharmaceutical and pharmaceutical manufacturing. Made from premium film, these bags offer ease of use and efficient product recovery for handling large fluid volumes. They are available in various sizes and can be used for buffer, media, intermediate, or drug substance mixing. Customizable configurations are available to meet specific process requirements. Manufactured under ISO 9001:2015 certified quality management systems and cGMP conditions, the bags undergo extensive testing to ensure compliance with pharmacopoeia standards and bio-compatibility. The specialized multilayer film used in XELTA Mix bags provides excellent chemical resistance, including polar solvents, and has favorable properties such as clarity, tensile strength, and gas permeability. Gamma irradiation is the recommended sterilization method for these bags.
The XELTA Mix bags allows user to order a wide range of configurations with choice of connectors, tubing, clamps, etc from any supplier for configuring the bags as per process requirements.
The XELTA Mix bags are designed, developed and manufactured in accordance with ISO 9001:2015 certified Quality Management System. They undergo extensive testing before shipping. We make sure our products are manufactured according to cGMP under ISO7 classroom conditions.
MORE SOLUTIONS
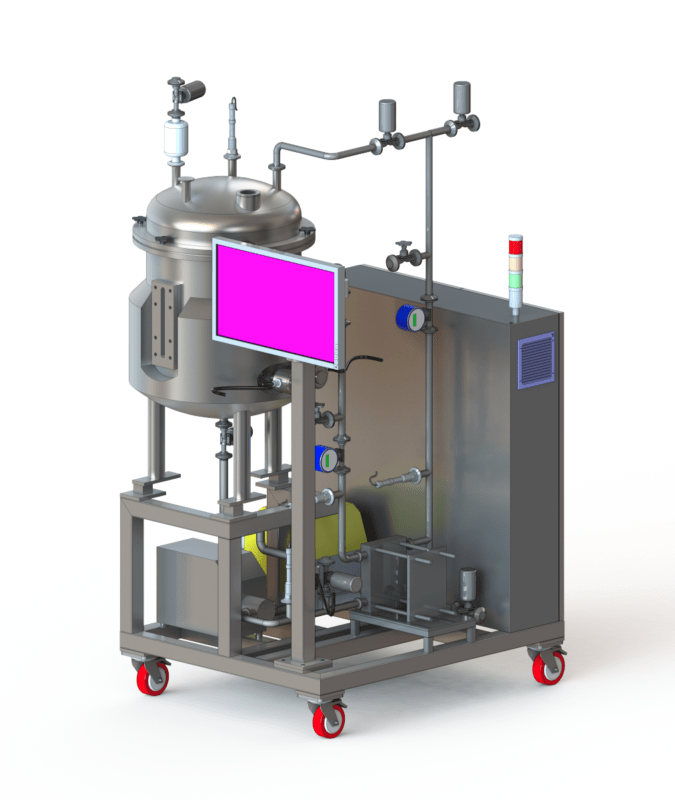
NXTtff
The NXT TFF system by PharmNXT Biotech is a system that’s perfect for running fully automated UF/DF processes at high capacity. It can handle any volume between 20L and 500L (200 g to 2.5 kg), and the compact system, has a low hold-up volume and the capacity to accommodate cassettes with surface area ranging from 0.5 to 2.5 m2
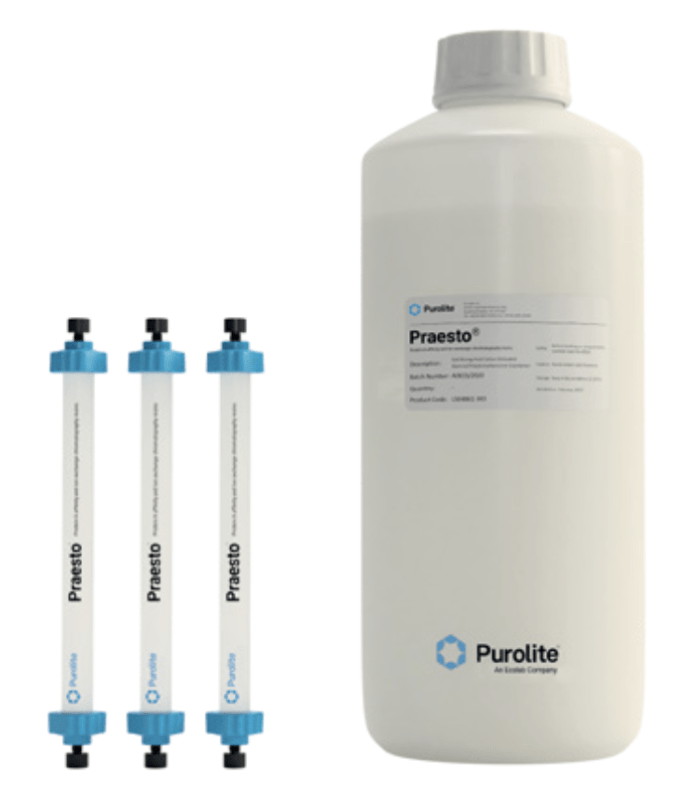
Chromatography Resins (Purolite)
The purification of commercially-available monoclonal antibodies (mAbs) on the market today is typically performed in three chromatography steps. Purolite offer industry-leading solutions for each step.
Protein A Affinity Chromatography
A Protein A affinity resin is utilized as an initial antibody capture step. Praesto Protein A resins deliver exceptionally high purity (>99%) and yield in a single, efficient step.
Cation Exchange Chromatography
A Sulphopropyl- (SP) functionalized cation exchange resin in ‘bind and elute’ mode is used to remove aggregates and HCP (Host Cell Proteins).
Anion Exchange Chromatography
A Quarternary Amine (Q) functionalized anion exchange resin is used in ‘flow-through’ mode to remove trace contaminates and ensure sufficient viral clearance.
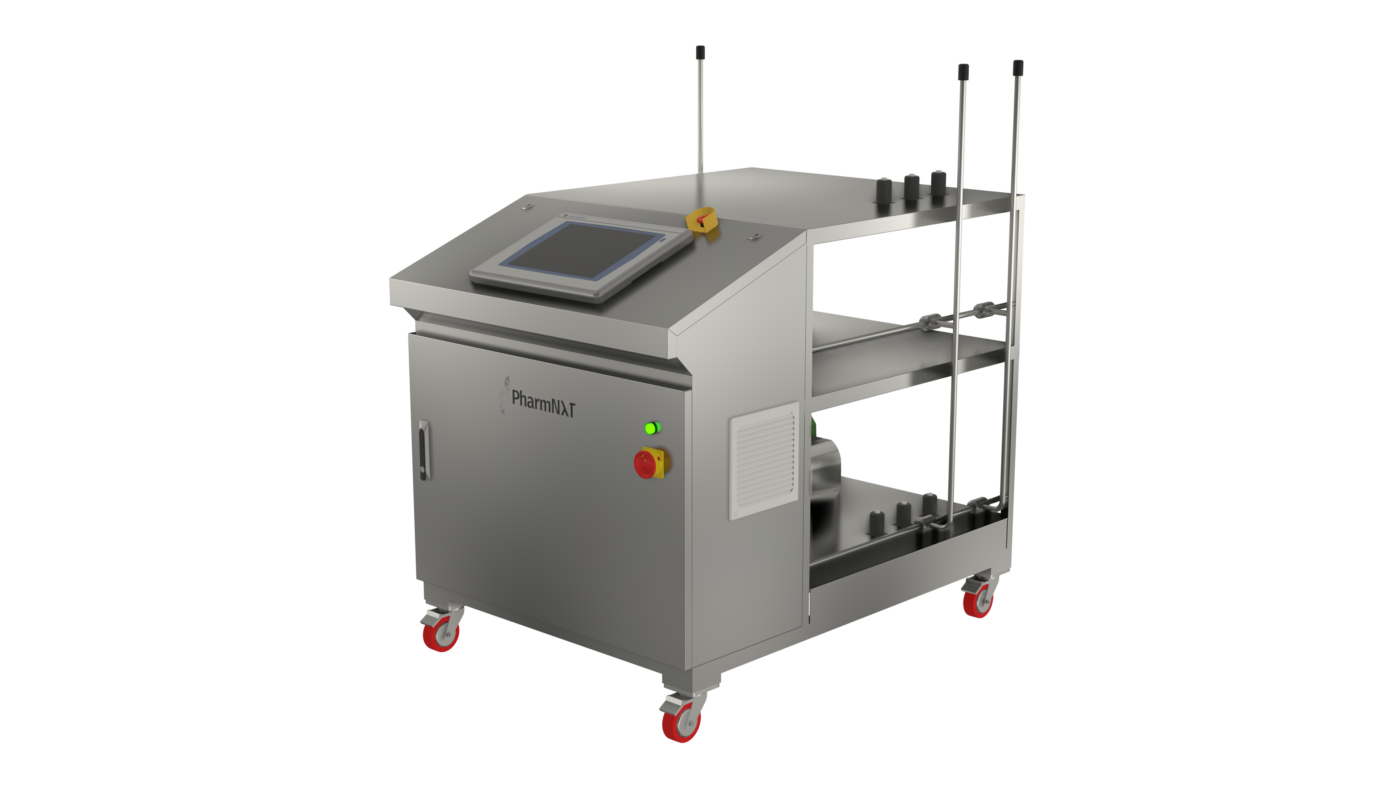
NXTmfilt
Single-use technology continues to be adopted for many areas of bioprocessing. The use of automation provides additional benefits in manufacturing such as consistency in product quality, reduced labor costs, and reduction of operator errors.